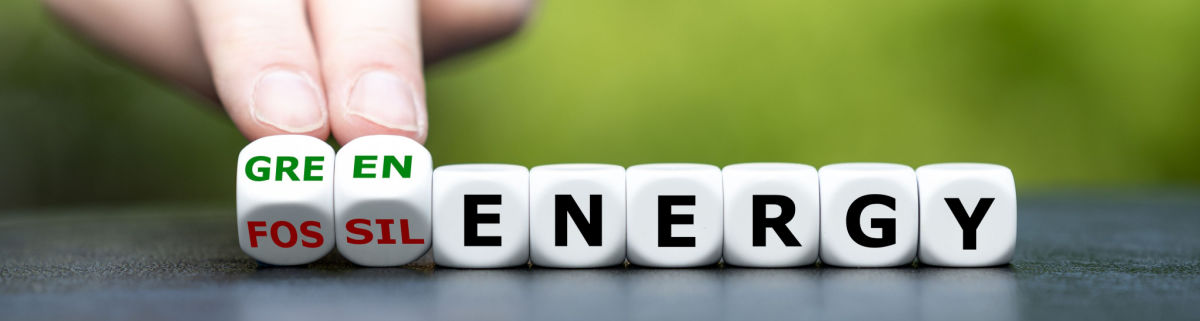
What Are Renewable Fuels
Renewable fuels are produced from plants or animal by-products such as vegetable oils, used cooking oils, and animal fats. These sources are considered renewable because the raw materials they are derived from can quickly be regrown, absorbing CO2 from the atmosphere as they do. Other potential feeds for renewable fuels are biomass and recycled plastic.
Benefits of Renewable Fuels
The renewable fuels produced today are different than “biofuels” such as biodiesel and ethanol. The product now referred to as Renewable Diesel (RD) is chemically identical to traditional ultra-low sulfur diesel (ULSD) made from petroleum. In addition to being “low carbon”, RD offers other advantages over fossil-derived diesel including a higher cetane number, a lower density, and a sulfur content approaching zero. Renewable diesel will actually enhance a refiner’s ULSD pool and, unlike biodiesel, there is no limit to the amount of RD that can be blended into the diesel pool. Renewable diesel offers up to an 80% reduction in greenhouse gas (GHG) emissions and does not require any modifications to conventional engines or the fuel supply infrastructure.
Renewable jet fuel, referred to as Sustainable Aviation Fuel or SAF, is also a drop in replacement for petroleum-derived jet fuel. SAF reduces the carbon footprint of the airline industry, lowering GHG emissions from jet aircraft by 60-80%. It also meets or exceeds all of the current jet fuel specifications and requires no changes to the jet engines already in use today.
How is Renewable Fuel Manufactured?
There are numerous technologies for producing renewable fuels including the HydroFlex™ Process from Topsoe and UOP’s Ecofining™ process. Regardless of the technology chosen, each starts with pre-treatment of the feed by washing, bleaching, and filtration to remove contaminants such as phosphorous, metals, chlorides, and nitrogen. If not removed, these contaminants will quickly poison catalysts used for processing the feed further downstream. Some renewable fuel facilities purchase feeds that have already been treated while others have units onsite to upgrade the quality of the feed material.
Pre-treated feed is then pumped into a reactor where triglyceride structures are broken down and oxygen is removed, yielding hydrocarbon chains that can be processed into liquid fuels. The processes involved in breaking down triglycerides are called hydrodeoxygenation (HDO) or decarboxylation (DCO). HDO is the preferential route because it produces a hydrocarbon chain with one additional carbon as compared to DCO. The other reaction by-products are propane and water. The DCO process yields a slightly shorter carbon chain since one of the carbons is converted to CO2.
Once oxygen is removed from the molecules via HDO, the product can then be hydrotreated to convert the carbon chains into normal paraffins in the boiling range of diesel, gasoline, or jet fuel. The final step is dewaxing or hydrocracking of these paraffins to improve the cold flow properties of the fuel. Dewaxing can be carried out in the same reactor as the hydrotreating catalyst (single-stage configuration) or in a separate reactor vessel (two-stage configuration). Dewaxing is essentially the same as mild hydrocracking.
How is Reactor Resources Helping to Produce Renewable Fuels?
The hydrotreating catalysts employed to produce renewable diesel and SAF are very similar to the catalysts used in traditional hydrotreaters processing petroleum fractions. Like their “fossil fuel cousins”, these renewable fuels catalysts are activated by sulfiding the metal oxides on the catalyst support with H2S. The thiochemical products we supply are used to create the H2S needed during the sulfiding (activation) operation.
In addition, since renewable feedstocks contain little or no sulfur, the refiner must continuously inject a spiking agent such as DMDS or TBPS to protect the active sulfides on the hydrotreating catalyst. In a unit processing fossil fuels, the feed contains plenty of sulfur to keep the catalyst fully sulfided and active. However, renewable feed stocks need the constant addition of sulfur to prevent desulfurization of the active sulfide structures, keeping the catalysts performing at their optimum level.
Reactor Resources has assisted with the startup of over a dozen renewable fuels units and supplies thiochemicals to numerous sites throughout the USA where significant quantities of “green fuels” are now produced. In addition, we have developed techniques that improved the selectivity of catalytic reactions involved in producing renewable fuels by the addition of nitrogen.
What’s Next for Renewable Fuels? Pyrolysis Oils
It’s estimated that if all of the available vegetable oil and animal fat was converted to renewable fuel, this could only replace 3% of the petroleum based fuel consumed in the USA. Therefore, renewable fuel producers will need to look for other feed streams that can reduce GHG emissions if they want to replace a larger portion of fossil derived fuels. One potential feed is called pyrolysis oil. Pyrolysis is the thermal degradation of biomass or plastic waste at temperatures in the range of 570 to 1650°F (300–900°C) in the absence of oxygen, producing a liquid oil. A variety of catalysts can be used to enhance the pyrolysis process such as ZSM-5, Y-zeolite, FCC, and MCM-41. Numerous reactions occur during pyrolysis including cracking, oligomerization, cyclization, aromatization and isomerization. After pyrolysis, the oil product undergoes hydroprocessing steps to remove metals, oxygen, nitrogen, and sulfur. Next is a catalytic hydrocracking step to covert the hydrotreated pyrolysis oil into various fuels. And finally, the product is fed to a fractionation column where it is separated into the desired fuel products.
The potential feed available for pyrolysis oil processing is much larger than the feeds now used to produce renewable fuels. For example, it’s estimated that the world now produces over 300 million tons per year of plastic, and this amount is expected to continue growing. Unfortunately, the contaminants contained in pyrolysis oil made from recycled plastic are extensive, causing the process to convert plastic into fuels to be a very expensive proposition.
Products and expertise from Reactor Resources will be in increasing demand as pyrolysis oil processing grows. The hydrotreating and hydrocracking catalysts utilized in this process will need to be activated with our thiochemicals, and the continuous addition of sulfur will also be required, similar to the constant addition of sulfur used with current renewable fuel processes.
Reactor Resources is uniquely positioned to assist our clients as they transition from fossil-derived fuels to “green energy”.
Learn More About Catalyst Sulfiding »
Contact Us for more details on the products and services we provide for the production of renewable diesel and sustainable aviation fuel.